Habitat for Humanity Debuts First Completed Home Constructed Via 3D Printer
Anyone who’s moved into a house built from the ground up knows that—especially in the middle of a pandemic—it can take anywhere from just a few weeks to a full year. But perhaps that sometimes torturous timeline is about to become both shorter and more predictable with the launch of Habitat for Humanity’s first 3D-printed house. The three-bedroom, two-bath concrete structure, which can withstand hurricanes and tornadoes, is a 1,200-square-foot technological triumph in Virginia whose exterior was constructed in just 28 hours using an Alquist 3D printer. The Tk-based company, headed by founder and CEO Zack Mannheimer, partnered with the nonprofit to construct the monumental project. “You don’t have to be a millionaire to customize your home. 3D technology allows for customization at all levels of home buying, and Alquist will be offering this later this year,” he explains.
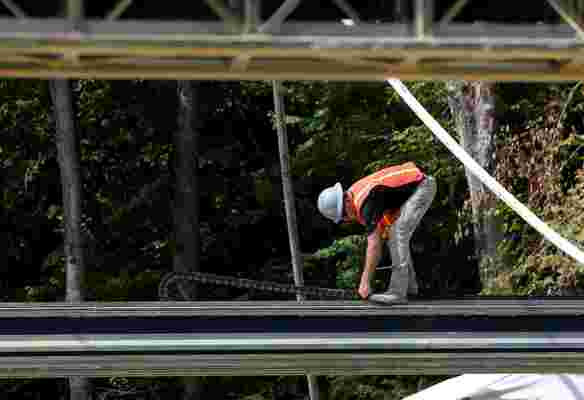
The newly minted homeowner, April Stringfield, bought her 3D-printed home through the Habitat Homebuyer program, which works with applicants who clarify their need for safe, affordable housing from community to community around the country. Over the winter holidays this year, Stringfield and her 13-year-old son got the keys to their quite literally groundbreaking home and moved in. It wasn’t so easy, though: Before moving in, Stringfield had to log a lot of “sweat equity” hours, which Habitat homeowners are required to perform after they’re accepted into the program. Luckily, it’s not as grueling as its name implies.
Stringfield had to either help build her home, which the 3D printer handled itself, enroll in homeownership classes, or volunteer at the Habitat ReStore. Janet V. Green, CEO of Habitat for Humanity Peninsula & Greater Williamsburg, admits, “We hope this new 3D technology will be another way to build more affordable homes for families with low to moderate income.”
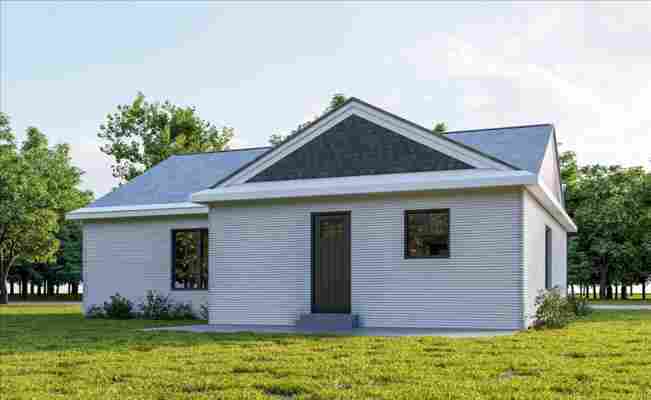
This is hardly Habitat’s first foray into the 3D printing sphere, though. The Virginia home follows a project that began earlier this spring in Tempe, Arizona. The house was constructed using both a Build on Demand printer (sent over from Germany-based Peri Group ) and more traditional building methods. However, unlike the Arizona home, Stringfield’s home in Virginia comes with her own personal 3D printer that will let her reprint just about anything from electrical outlets to cabinet knobs. Mannheimer adds, “Habitat and Alquist share a similar mission: building housing that is affordable. We both believe in the American Dream of homeownership, and, by partnering, we can realize this dream for more families.”
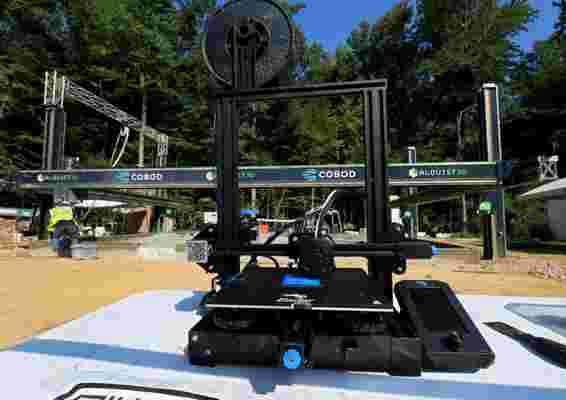
Though efficiency is certainly of the essence when it comes to everything Habitat for Humanity does, sustainability is equally as important. And this highly technical home is hardly an exception. In fact, it’s EarthCraft certified, which basically provides a blueprint for building comfortable homes that both reduce utility bill costs and minimize negative environmental impacts. “3DCP (3D concrete printing) reduces the amount of waste that is typically found on a jobsite, and our energy savings are significant. Still, concrete is far from the most environmentally friendly material, and we are working with partners to create a greener material in the next year,” Mannheimer explains. And the collaborative project in Virginia is just the first of many new homes—built in record speed—that will be popping up across the country within the coming years.