Ole Sondresen on his Manufacturing Innovation Hub for Apparel, Textiles & Wearable Tech
This summer construction will begin on the Manufacturing Innovation Hub for Apparel, Textiles & Wearable Tech, a new fashion center in Sunset Park, Brooklyn. With a $3.5 million grant from the City of New York, Ole Sondresen Architect will redesign the fifth floor of the Liberty View Industrial Plaza to host a small factory for sample making, a work-development center, design studios, a research and development center for wearable technology, and the headquarters of fashion design and production incubator Manufacture New York.
Architectural Digest spoke with Sondresen about his plans for the space.
Architectural Digest: What attracted you to the project?
__Ole Sondresen:__In addition to the architectural challenge—it’s not just manufacturing, but an incubator space, a tech annex, and more—the facility is bringing small-scale manufacturing and small-run productions back to New York City. It’s a great concept for all industries, but especially for fashion. Many small designers can’t get off the ground because they don’t have anywhere to make their first runs, so they end up going abroad. Bringing manufacturing back here gives these designers an opportunity to launch their brand and creates more jobs in the industry.
AD: Did you find it difficult to incorporate so many functions into one design?
__OS:__No, I think they’re all very symbiotic. It’s like building a little village that’s home to thinkers, designers, inventors, and tradespeople. All of these complex programs and their diverse needs give us the opportunity to make something unique.
__ AD: __At 160,000 square feet, the hub is one of the largest spaces your firm has designed. What was your approach?
__OS:__That’s where our concept of a village comes in. Each program is like its own building, but they all share an aesthetic. They are linked by an internal kind of “Main Street” that brings light through the programs’ suites. It’s wide enough to encourage mingling, and we put the food court there, too. We also set it up to accommodate runway shows.
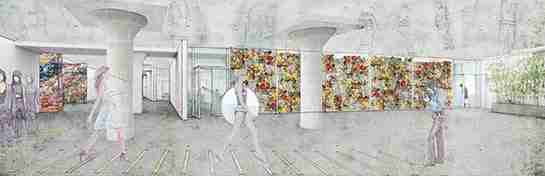
__ AD: __Your practice is heavily focused on sustainability; how did you incorporate that into the design?
__OS:__This is going to be a LEED-certified project. Not only is the design sustainable, but the construction of it will be as well, creating a better environment for the workers who are actually building the space. We’ve covered everything from indoor air quality to use of reclaimed materials to energy-efficient lighting systems. Our office always tries to work with local vendors and suppliers. It’s one of the reasons we get along so well with the Manufacture New York team. On an industrial manufacturing scale, they’re trying to support small or medium-size local designers and manufacturers. For us, that’s the fundamental principle of sustainability.
AD: You’re no stranger to working with creative businesses—you’ve designed spaces for companies like Kickstarter and Etsy. How do you think your designs influence the innovators who inhabit them?
OS: We’re all influenced by our work environment. That said, there are people who do great things in dark basements. A light-filled space is not a must to be a creative genius, but I think it’s more inspiring to be in an office that doesn’t just look good, but sounds, smells, and feels good too.
AD: Did you learn anything new from doing this project?
OS: We’re just in the beginning phases, but there are many learning opportunities. I think the increase in project size will be very interesting. We wonder how we, as design architects, can make a positive impact on a manufacturing space. How much influence do we have? How can we control acoustics and fresh air?