These Prefabricated Homes Showcase the Beauty and Innovative of Sustainable Living
Prefab housing has come a long way from the days of Sears Catalog homes —and it may just hold the answer to many of our modern housing woes, including the need for affordable and sustainable living spaces. “Building a home in a factory environment gives the fabricator better control over the end product and improves management of the resources used in construction,” says Avi Friedman, a professor of architecture at McGill University. “In addition, I found out that a significant amount of time can be saved on site, which can also contribute to cost reduction.” In his new book Pre-Fab Living (Thames & Hudson, $40) , Friedman explores the latest advancements in prefabricated housing and showcases projects that show just how beautiful and innovative these dwellings can be. “The designs in the book are very attractive, in addition to being economic and very fast to build,” he says. While prefab could be the wave of the future, Friedman says that for this method to become more widespread, it will require investment in prefabrication plants, the building of demonstration projects, and making the public realize the benefits. “In the past, prefabricated homes were stigmatized for their bad appearance,” the architect says. “I selected buildings that demonstrate how aesthetically pleasing a prefab home can be.” Read on to see homes that are sure to change the way you see prefab.
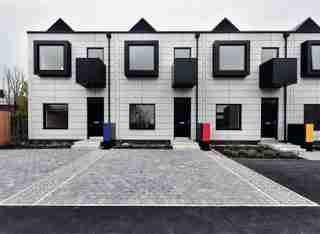
Town House (Manchester, United Kingdom)
Made up of 36 row houses, the Town House development recalls traditional terrace homes but with a graphic twist: The dwellings, which were designed by ShedKM, can be completed within two to three weeks.
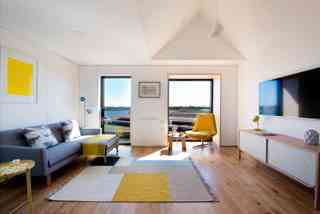
Town House (Manchester, United Kingdom)
While locations of the kitchen and bathrooms are set, clients can customize the layouts to fit their needs, including open or traditional floor plans, and add amenities such as balconies, gardens, and parking.
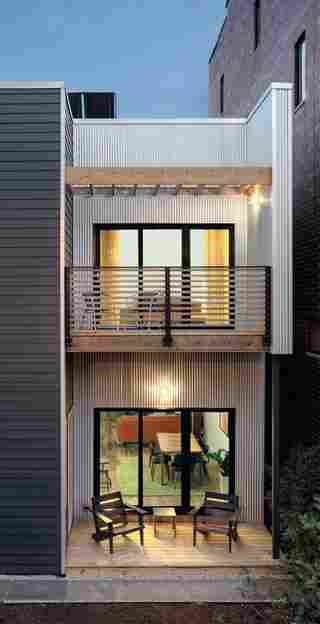
C3 Prefab (Chicago)
Architect Jeffrey Sommers of Square Root designed the semi-customizable C3 Pre-fab—the first LEED Platinum–certified home in Chicago—using corrugated Galvalume, reclaimed wood, and fiber cement. Modular construction allowed the firm to build on a narrow site that would have not have allowed traditional building methods.
C3 Prefab (Chicago)
The home incorporates an array of sustainable elements, such as a water-catchment system, solar thermal panels, and a living roof. Recycled and reclaimed materials, such as recycled gypsum boards and reclaimed engineered hickory floors, were used for the interior.
Smallhouse (Switzerland)
Bauart Architekten’s two-story wood-framed Smallhouse can be assembled in one day on-site and features four panoramic windows—one for each zone in the home. The compact design’s layout can be customized to include an interior atrium, and future additions can easily be incorporated.
Sonoma weeHouse (Santa Rosa, California)
Comprising two prefab corrugated steel boxes on concrete plinths, Alchemy Architects’ Sonoma weeHouse takes full advantage of its hillside location. The main home includes a central “bed box” separating the living room and bathroom, and the other structure serves as a guest house.
Sonoma weeHouse (Santa Rosa, California)
The main house and its porch were shipped nearly complete and each element was cantilevered onto the site. Sliding glass walls provide access to sweeping views of the landscape.
The Stack (New York City)
Architecture firm Gluck+ devised this building—the first prefab, multiunit residential structure in New York—as a solution to the lack of moderate-income housing in the city. The seven-story building was manufactured in Pennsylvania and on-site installation was completed in just four weeks.
The Stack (New York City)
The building includes commercial space on the ground level; above, 56 modules make up 28 apartments, ranging from studios to three-bedroom units. The interiors were designed with durability in mind and feature materials such as Corian counters, concrete floors, and aluminum windows.
Tim Palen Studio at Shadow Mountain (San Bernardino, California)
Ecotech Design built this prototype hybrid house in the Mojave Desert using six shipping containers, which were fabricated in Los Angeles, then stacked in pairs at the site. Five containers are home to living spaces and the sixth is connected to the photography studio and provides equipment storage.
Tim Palen Studio at Shadow Mountain (San Bernardino, California)
The house was built at half the cost of other prefab homes in the area, and thanks to the firm’s attention to energy efficiency, it exceeds the state’s energy code requirements by an impressive 50%. The building is topped with a modular living roof with native plants to absorb heat, glare, and CO2.
Pre-Fab Living (Thames & Hudson, $40)